Encapsulation plant
Spent fuel is safely sealed in the disposal canisters at the encapsulation plant. The encapsulation plant developed by Posiva has a lot of unique technology, but the design has utilised experience from fuel processing plants designed in different parts of the world. There are differences in the solutions of different countries, such as whether fuel elements are dismantled or placed as such inside the canister. In Finland, the elements are not dismantled, only sealed in the canister.
The fuel assemblies weighing a quarter of a tonne each provide energy for the reactors of Olkiluoto nuclear power plants for approximately four years. Spent uranium fuel is highly radioactive after its removal from the reactor, but its radiation level will decrease to one-hundredth already within the first year. First, fuel assemblies are cooled in the reactor building’s water pools before they are transferred to the interim storage.
The fuel assemblies are then transferred from the reactor building to the interim storage for spent fuel located in the plant area. There, the temperature and activity of the assemblies will continue to decrease. Upon final disposal, when approximately 40 years have passed from the removal of spent fuel from the reactor, it will retain only 1/1,000 of its original radioactivity level. Upon final disposal, the canister walls and a few metres of rock are enough to stop the radiation released by spent fuel entirely.
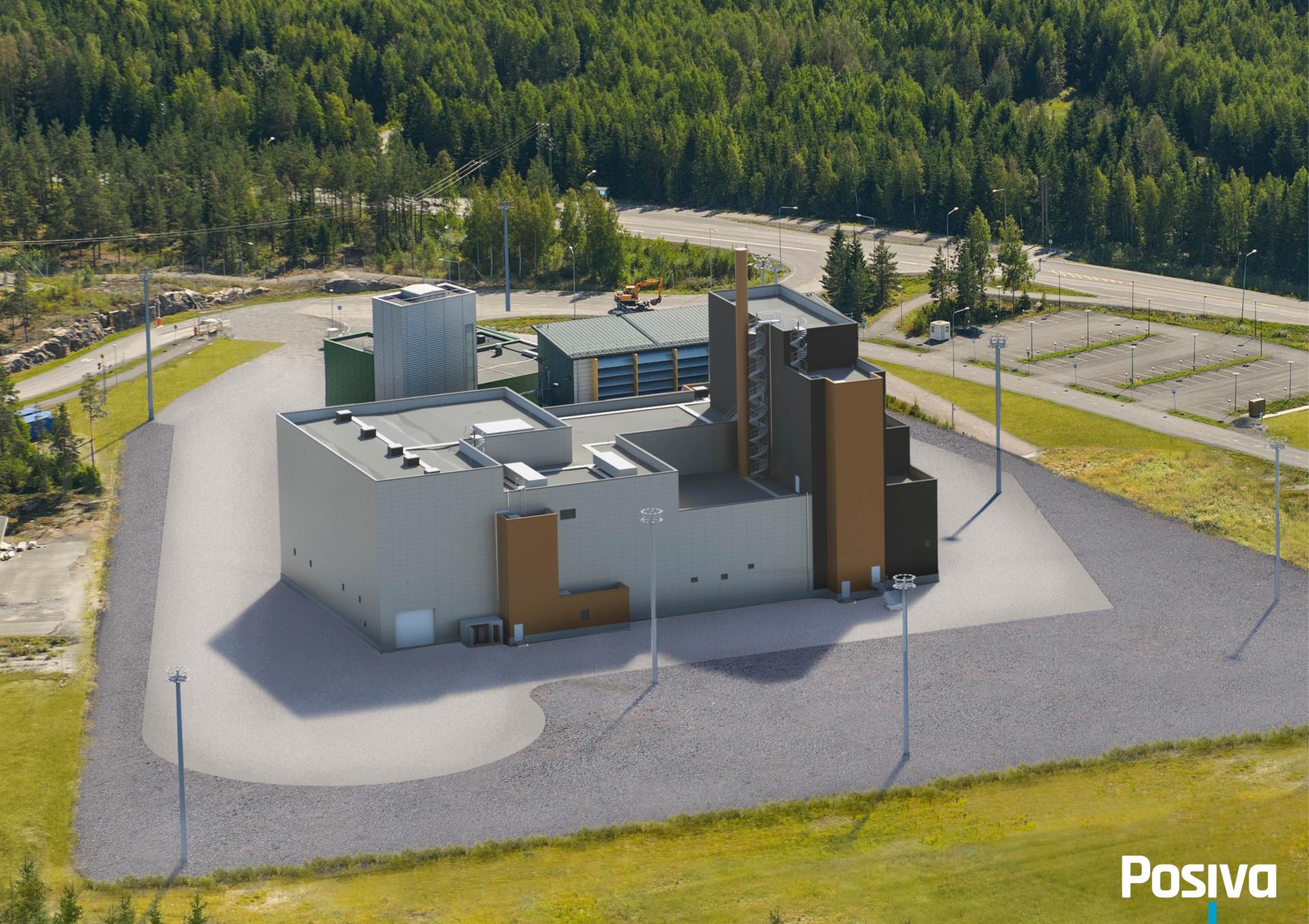
The construction of the encapsulation plant started in 2019. The plant will host a great number of equipment and technology that is not used anywhere else in the world.
When final disposal operations are underway, spent fuel is brought from the interim storage to the encapsulation plant for packing in the final disposal canisters made of copper and spheroidal graphite cast iron. The encapsulation plant is connected to the underground disposal facility by means of a canister lift, which transports the canisters down to the deposition level at a depth of 430 m to the underground reception station. From there, they are transported with the transfer and installation vehicle to the deposition tunnels.
In the encapsulation plant, the final disposal canister is moved in the different work phases in the underground rooms of the capsulation plant. Spent nuclear fuel is loaded into the final disposal canisters in the fuel handling cell, the concrete walls of which are approx. 1.3 m thick. Once all fuel assemblies have been transferred inside the canister, it is filled with argon gas and sealed tightly with the inner steel lid of the canister. The top copper lid of the canister is sealed by means of friction stud welding in the welding chamber, and the tightness of the joint is checked both visually and by means of an eddy current and ultrasonic inspection. Friction stud welding chosen for welding forms a joint seam on the copper lid so that the integrity of the seam corresponds to the integrity of the canister shell. Posiva has developed the method together with the Swedish Nuclear Fuel and Waste Management Company, SKB.
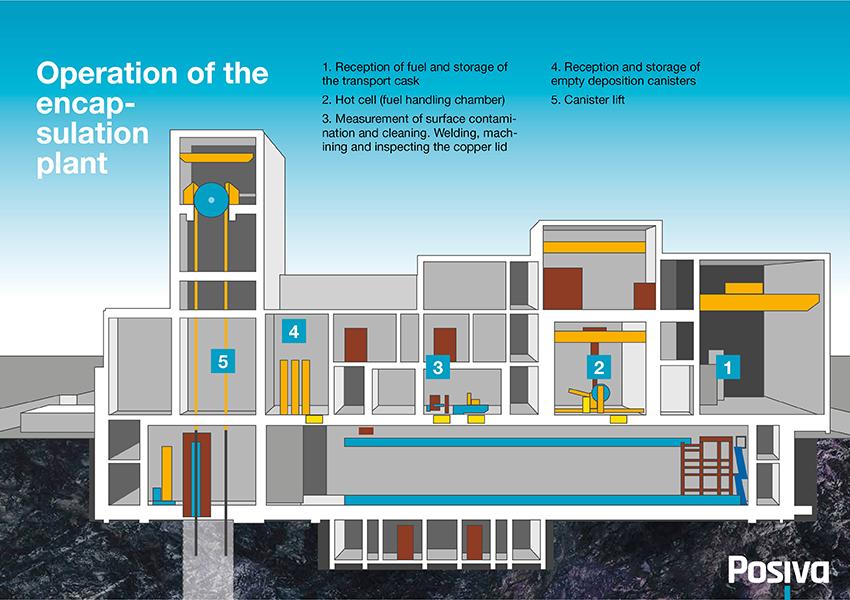
The encapsulation plant in numbers
- The building’s length is approx. 72 m and width approx. 40 m.
- The building’s surface area is approx. 3,000 m2, floor area approx. 11,500 m2 and volume approx. 70,000 m3. For example, the total volume of Turku Castle is approx. 60,000 m3.
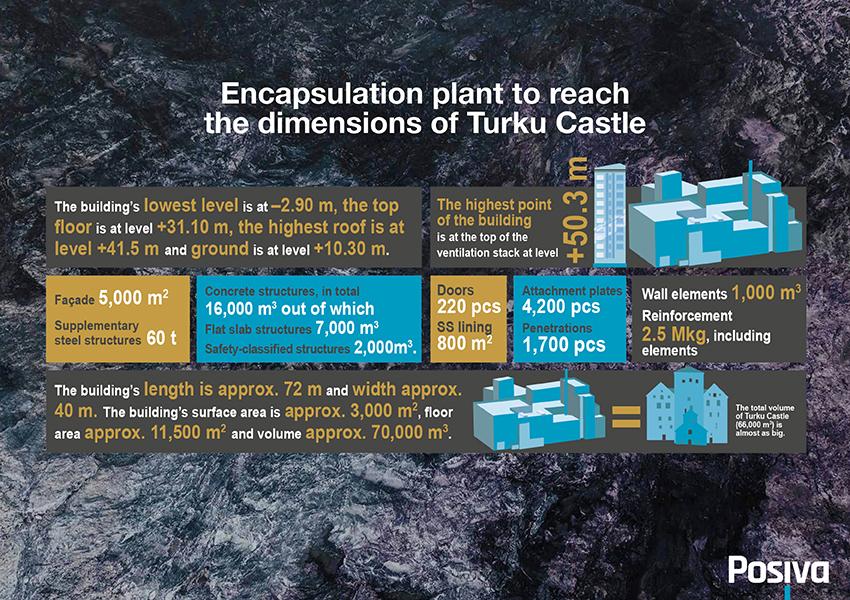