Encapsulation plant’s friction stir welding system to be supplied by Bond Technologies
28.10.2019
Posiva is acquiring a friction stir welding system for sealing disposal canister copper lids from US Company Bond Technologies.
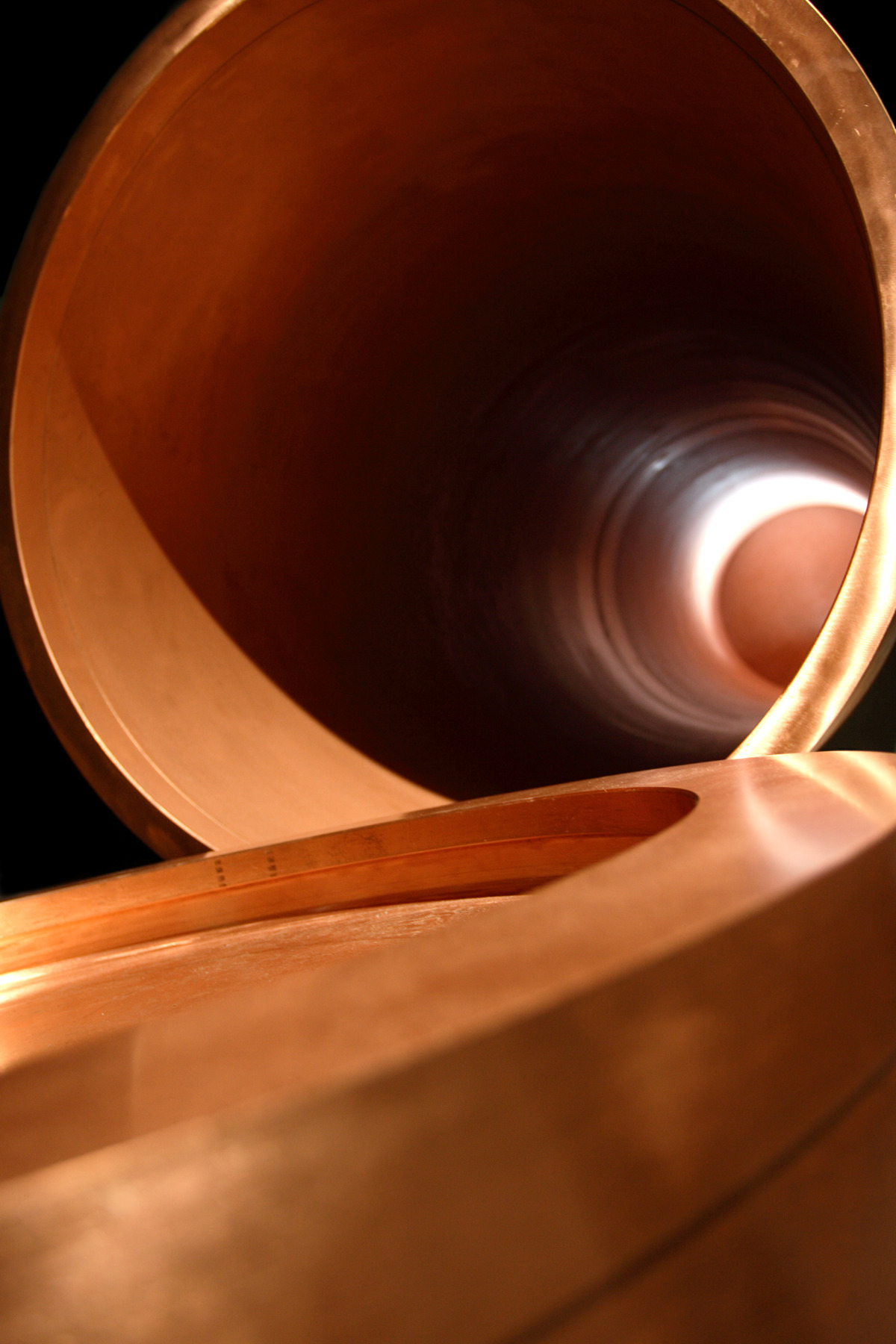
The contract scope includes the manufacture, installation and commissioning of the friction stir welding equipment. The system is an important and critical part of the production process of the encapsulation plant.
- We are extremely pleased that, after long contract negotiations, the system designer Bond Technologies was also selected as the equipment manufacturer and supplier, says Program Manager Iiro Engren.
Posiva has developed a friction stir welding system
in collaboration with the Swedish Nuclear Fuel and Waste Management Company
(Svensk Kärnbränslehantering AB, SKB). Both companies have selected the system
as their canister sealing solution. Posiva and Bond Technologies designed and developed the
welding device, which is now under manufacture, during an earlier design stage
of the project.
Spent nuclear fuel is packed in copper and cast-iron
canisters before its deposition in bedrock. The metal canister is the most
important engineered barrier of the disposal concept. The canister’s copper shell
consists of a copper tube with an integrated or welded bottom, depending on the
manufacturing method, and a copper lid that is welded to the canister at the
encapsulation plant. The properties of the weld must not significantly deviate
from the properties of the base material.
Friction
stir welding is based on hot forming, where the required temperature is caused
by friction of a tool rotating with high speed in the material to be welded.
Friction stir welding meets the requirements of long-term safety very well,
since its benefits include small grain size in the weld area, even and
isotropic grain structure as well as good mechanical properties and
microstructure that are suited to the disposal canister.
Share