Here’s how the clay buffer installation system works as part of final disposal
Did you know that Posiva’s final disposal of spent nuclear fuel deep underground uses various unique pieces of equipment that were specifically developed just for Posiva? One of them is the clay buffer installation system. The system comprises an installation unit, a transfer unit and transport containers. The installation unit and transfer unit move with the help of AGV vehicle platforms.
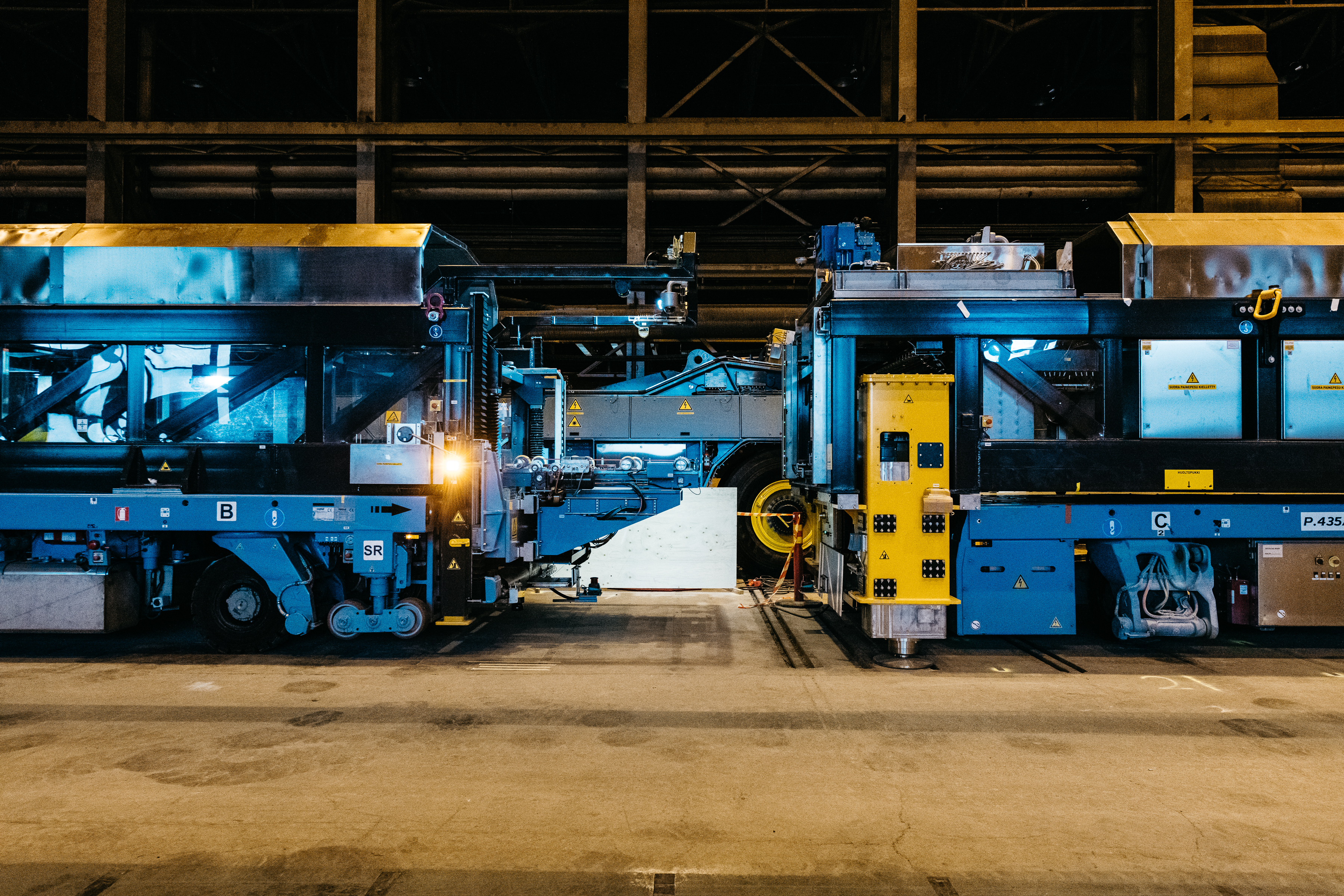
The clay buffer installation system comprises an installation unit, a transfer unit and transport containers.
The system is used for installing buffer system components made of bentonite clay into the 8-metre deep deposition hole that has a diameter of 1.75 m. The components include a layer to level out the bottom of the deposition hole, the buffer blocks installed under, around and on top of the canister and the sand-like, fine granular bentonite clay that fills the spaces between the canister, buffer blocks and bedrock. A final disposal canister has a diameter of 1.05 m.
Result of years of development
Posiva has been developing the system for several years. The world’s first buffer installation system to be used in the final disposal of spent nuclear fuel was designed, manufactured and assembled entirely by Finnish specialists.
Factory testing of the installation and transfer equipment, which verified that the system functions manually, was performed in Parkano in early June. Automation and communication systems that are required for the remote operation of the equipment have been built at a testing station in Pori.
In the video you can see the testing of the installation system of the clay bumbertransfer system retrieves clay buffers from the transport container and transports them to the installation device. All movements take place remotely and partially autonomously, guided by the navigation system.
The test of levelling the bottom of a deposition hole was also completed at the testing station in Pori. This test verified that the installation unit can deliver a sufficiently even granule layer on the bottom of a deposition hole. The bottom affects the straightness of the installed final disposal canister. This test only involved installing the buffer system components that are installed under a canister.
– Underground production equipment is now undergoing its commissioning and finalisation stage, during which the equipment is being integrated into the nuclear facility’s automatic control system, explains Ari Maarni, Development Manager at Posiva.
– The test operation of the disposal facility is currently under way, and the current stages must be completed successfully before we can proceed with the underground tests. This is necessary for ensuring personal and nuclear safety.
Autonomous movement underground
Posiva’s equipment is installed on AGV vehicle platforms that navigate autonomously around the disposal repository. They are fitted with extensive remote operation and automation technologies, including computer vision, laser sensors and cameras.
Other underground production equipment used by Posiva includes the deposition hole boring machine, the tunnel backfill installation system and the canister transfer and installation vehicle. Equipment tests and its integration into the complete final disposal system is progressing, and the performance of each piece of equipment will be demonstrated over the course of the current test operation.
Posiva Oy is the leading final disposal operator in the world, preparing to start in the mid 2020’s the final disposal of spent nuclear fuel in the ONKALO® facility excavated deep in the bedrock.
Story by Pasi Tuohimaa, photos: Tapani Karjanlahti
Share