First casting blank of final disposal canister ready for production
There it is, Posiva’s first casting blank in copper, waiting to be worked into an actual final disposal canister. Posiva has taken yet another significant step toward the start of the final disposal of spent nuclear fuel by completing the successful casting of the cylindrical, impressive casting blank just before the Mid-summer.
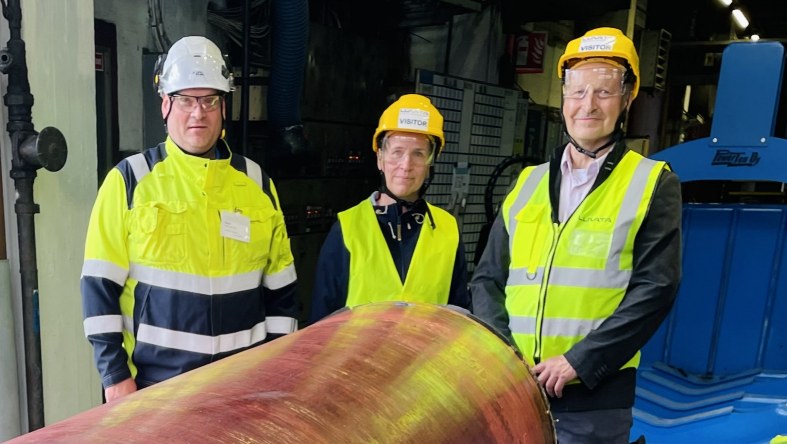
The first casting blank is finally ready. The massive, fresh out of the line copper casting is reviewed by quality control engineer Teppo Uusi-Uola, canister system owner Terhi Glas and canister manufacture coordinator Jouko Lammi from Posiva.
The casting campaign of the first six blanks has been started at Luvata’s plant in Pori. The Radiation and Nuclear Safety Authority of Finland (STUK) was also present to oversee the casting process.
The casting of the blank was completed during one shift. A preliminary analysis sample was taken of the casting before it was measured and weighed. The cast blank will next be transferred to the sawing process where its front and rear end are sawn to measure and official sample slices are cut for a material analysis.
The casting campaign of the first six blanks has been started at Luvata’s plant in Pori. The Radiation and Nuclear Safety Authority of Finland (STUK) was also present to oversee the casting process.
The casting of the blank was completed during one shift. A preliminary analysis sample was taken of the casting before it was measured and weighed. The cast blank will next be transferred to the sawing process where its front and rear end are sawn to measure and official sample slices are cut for a material analysis.
- The casting process was a great success. A good casting quality is important for the subsequent canister production phases. New investments have been made in the foundry to improve the quality and the processing of the casting. One of the most important accomplishments has been the increase in the diameter of the casting with a larger gravity die, explains Jouko Lammi, who is the canister manufacture coordinator at Posiva.
Casting blank of 17 tons of copper
After the sawing process, the casting blank will have its surfaces machined. At the next step, the casting blank machined to measure undergoes non-destructive testing (NDT); a visual inspection and a dye penetrant inspection.
The final step is Posiva’s inspection of the casting and the associated documentation. When the casting has passed the inspection, it is packed ready for transport for delivery to the cylinder manufacturer.
The original weight of the casting blank is over 17 tons of copper and the final delivery weight for cylinder manufacture is about 12 tons.
The copper cylinder produced from the casting blank forms together with the copper bottom and cover that are welded onto it a leak-tight copper canister with five-centimetre thick walls. In final disposal, the canister acts as a corrosion barrier for the canister insert made of cast iron. The insert accommodates 12 fuel elements.
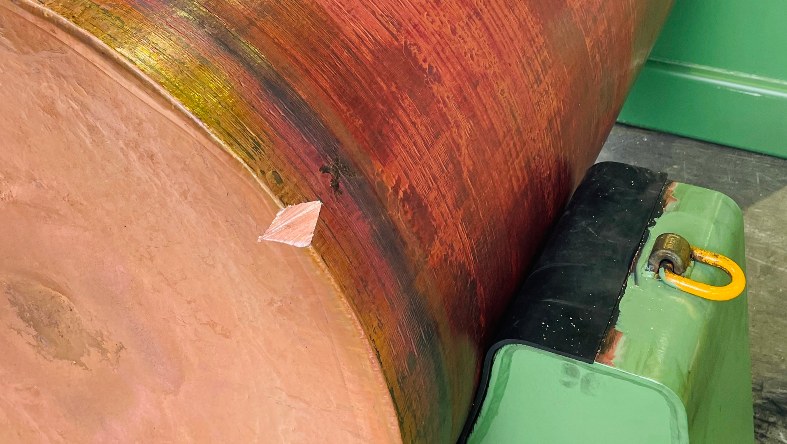
Text and photo: Pasi Tuohimaa
Share