Remote-controlled movers operate between canister storages and canister lift
After welding and machining, the finished final disposal canister is transferred into storage at the encapsulation plant by a remote-controlled mover. Later the same mover will retrieve the canister from the storage into the canister lift for transport to a depth of 430 metres. Another mover transfers the canister from the underground lift station again to storage where it stays until it is transferred to the actual deposition hole.
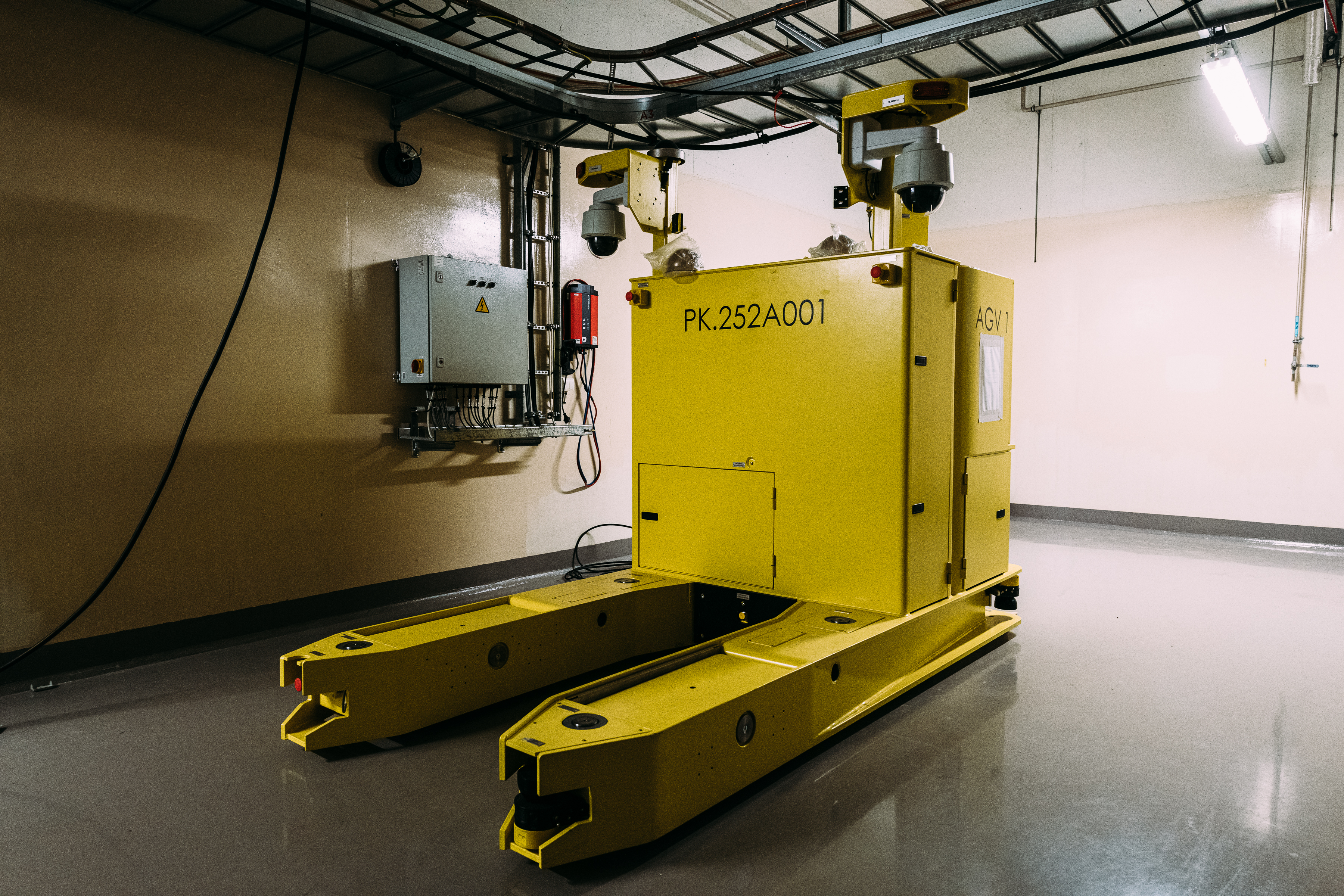
The mover weighs 4.7 tons and is capable of lifting loads of up to 30 tons. It has a maximum speed of 0.1 metres per second when carrying a canister, and 0.2 metres per second without a load. The mover is 3 metres long, 1.35 metres wide and has an overall height of 2.2 metres from the floor to the antenna. This crucially important transfer device is manufactured by the Finnish company Ab Solving Oy which is based in Pietarsaari.
According to Posiva’s System Owner Tommi Ristimäki, the battery-operated canister mover can navigate autonomously inside the plant. The canister storages are the only places where it is operated under remote control from the control room of the encapsulation plant.
The movers are also provided with towing equipment. This means that in the event a mover stops working at some point for some reason, it can be towed away be another mover, Ristimäki says.
At present, Posiva has two identical canister movers, one operating above ground in the encapsulation plant and the other in the underground canister storage. A third mover is expected to be delivered to Olkiluoto in the autumn.
Trial Run ensures safety of final disposal
Posiva’s Trial Run of Final Disposal is still ongoing with the last, the fifth canister now in turn. Part of the finished canisters have already been transferred by the canister lift into the underground canister storage. As part of the Trial Run, one canister has also been retrieved back to the ground surface.
The final stage of the Trial Run later this year will take place underground and focus on the test operation of the final disposal repository excavated in the bedrock. This will involve tests on technology and operating procedures in ONKALO® at a depth of about 430 metres.
The final disposal canisters are transferred from the underground storage to the deposition holes and enclosed in a bentonite backfill. Some unique technology has been developed for the transfer and the bentonite backfill process as well. An example is the canister transfer and installation vehicle which is 12.5 m long and weighs 87 tons. The test operation deep in the bedrock will demonstrate the operating capacity of the equipment.
Before the canister is placed in the deposition hole, blocks made of bentonite clay are installed with the buffer block installation system. The final disposal canister does not come into direct contact with the bedrock at any point, but is surrounded with bentonite installed beneath, on top and on all sides of the canister. When the bentonite swells, it forms a tight buffer between the canister and the bedrock.
Once all four (the fifth has been returned to ground surface) test canisters have been placed in the deposition holes, the corridor is filled with granular bentonite and sealed with a reinforced concrete plug – in exactly the same way as in the actual final disposal process.
Instead of actual spent nuclear fuel, the Trial Run is conducted using non-radioactive test elements. The purpose of the Trial Run of Final Disposal is to demonstrate the functionality of the final disposal process as a whole and the readiness of the personnel for industrial final disposal operation. The Trial Run started in August 2024.
Text: Pasi Tuohimaa
Picture and video: Tapani Karjanlahti
Share